What is IoT in Manufacturing ?
IoT in manufacturing helps manufacturing units in improving their manufactured product quality, increasing productivity, and reducing manufacturing costs. It is one of the driving technologies behind the industry 4.0 revolution. IoT in manufacturing is adding value to the entire manufacturing value chain from forecasting to product in the hands of customers.
In this article, we will discuss “what is the industrial internet of Things“, the advantages, and applications of IoT in manufacturing.
What is the Industrial Internet of Things ?
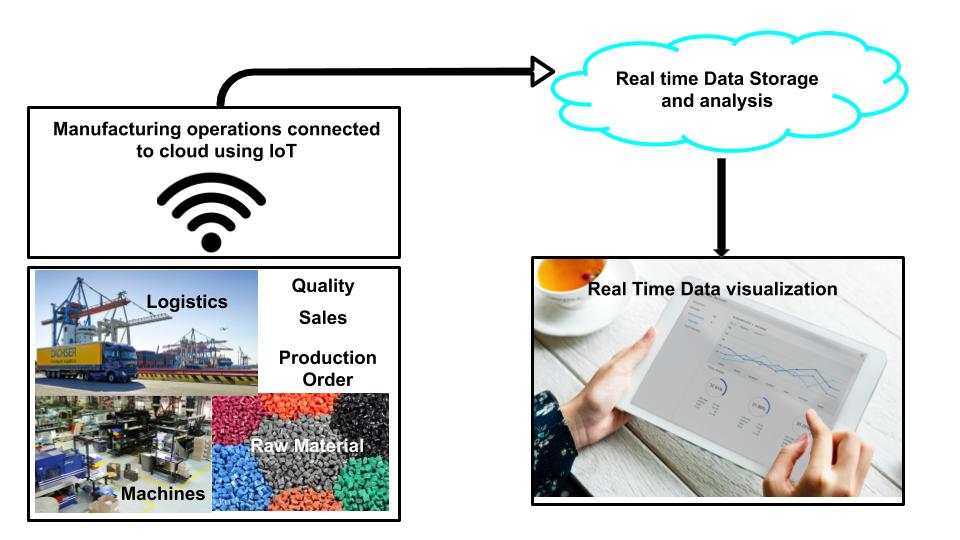
“Industrial Internet of Things” connects entire manufacturing operations with a network of sensors to collect the manufacturing data and sends it to the cloud.
In the cloud, machine learning algorithms and artificial intelligence systems analyze this data to provide useful insights to the users.
Applications of IoT in Manufacturing Industry
- IoT in manufacturing activities
- Production Process Planning
- Oversight on Equipment Utilization
- Part Quality Control
- Preventive Maintenance
- Resource and Inventory Management
- Inventory Management
- Factory Asset Management
- Effective Resource Utilization
- Restricted Access Control
- Supply Chain Management
One by one we will discuss the above applications of IoT in manufacturing with examples.
1. IoT in the manufacturing Activities
IoT in production or manufacturing activities is used by connecting the machines with various types of sensors such as temperature sensors, Proximity sensors, pressure, and vibration, etc. These connected sensors send real-time machine data to the cloud.

Real-time connected machine data is analyzed and can be used in the following ways.
- Production process planning.
- Oversight in equipment utilization.
- Manufactured part quality control
- Machine preventive maintenance
IoT for Production Process Planning
Planning engineers can use real-time production and machine data to plan production activities for effective machine utilization.

Production activities are interdependent on one another. If one station stops, it has an impact on other stations as well. In case of any breakdown real time data helps production engineers to reschedule the activities.
Oversight on Equipment Utilization
IoT in the manufacturing industry is used to provide insight into real-time equipment utilization. This insight plays a key role in the effective utilization of resources. Therefore this real-time machine data from IoT sensors can be used for:
- Planning the purchase of new equipment.
- Improving utilization of existing equipment.
- Calculate Machine ROI (Return on Investment).
Part Quality Control in Manufacturing using Internet of Things

Manufactured part quality depends on process parameters and environmental conditions. IoT-connected sensors are used to monitor manufacturing process parameters continuously. If any variation in process parameters is observed, an alert is sent to the operator.
As a result, the operator takes corrective action before the part deviates from the acceptance limit. In this way, IoT is used in production to monitor and control manufactured part quality continuously.
Machine Preventive Maintenance
IoT in production is used to suggest preventive maintenance schedules for machines by sending real-time machine sensor data to the cloud. From where service engineers can monitor and analyze real-time machine sensor data and prepare machine maintenance schedules.

In the cloud, machine learning algorithms are also used to analyze machine data and suggest predictive maintenance schedules for machines.
2. IoT in manufacturing for Resource and Inventory Tracking
IoT in the Manufacturing industry is used to track factory assets, resources, and inventory inside & outside the factory premises. To track an asset IoT based tracking devices are attached with the assets or inventory. Each tracker has a unique ID that defines that asset. RFID tags, Bluetooth beacons, GPS trackers, barcode tracking technologies are used to track assets.
For indoor tracking, IoT-enabled receivers and scanners are installed inside factory premises. They send real-time IoT tracker positions to the cloud. From where this data can be accessed using an internet-connected device. Whereas for outdoor tracking, IoT-enabled GPS tracking devices are used. Real-time GPS data is sent to the cloud using GSM technology.
Asset and resource tracking in manufacturing can have the following applications.
- Inventory management.
- Factory asset management.
- Effective utilization of resources.
- Restricted Access control.
Inventory Management
In large factories or warehouses, It is very difficult to track an asset’s current location. Conventionally it is done manually and inventory location is entered in the ERP system or Microsoft Excel sheet that is prone to errors.
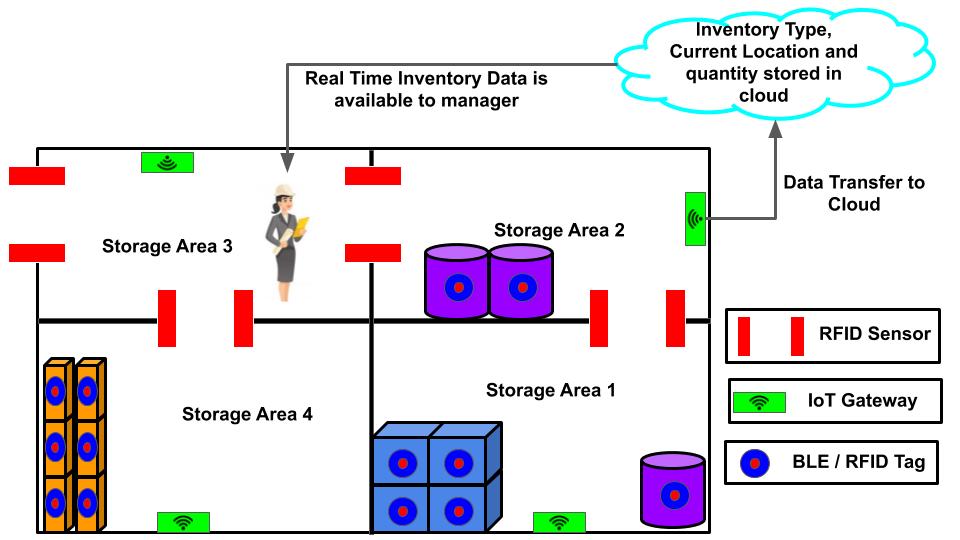
To automate inventory management processes, RFID tags or BLE beacons are attached to the inventory. IoT connected tags send inventory current location to the cloud. This enables automatic update of inventory location in ERP.
IoT in Factory Asset Management
IoT sensors are used in tracking moving assets such as cranes, measurement instruments, etc. in factory premises.

As shown in the above image, inside a large factory where carts and cranes move all around the factory to transport goods from one place to another. Industrial Internet of Things solutions can help managers to track asset’s real-time location for their effective utilization.
For indoor premises tracking BLE beacon and RFID technology are used. Whereas for outdoor tracking, GPS trackers are used.
IoT for effective utilization Resource
The IoT-enabled solutions play a key role in the effective utilization of resources that is essential to increase overall manufacturing productivity.
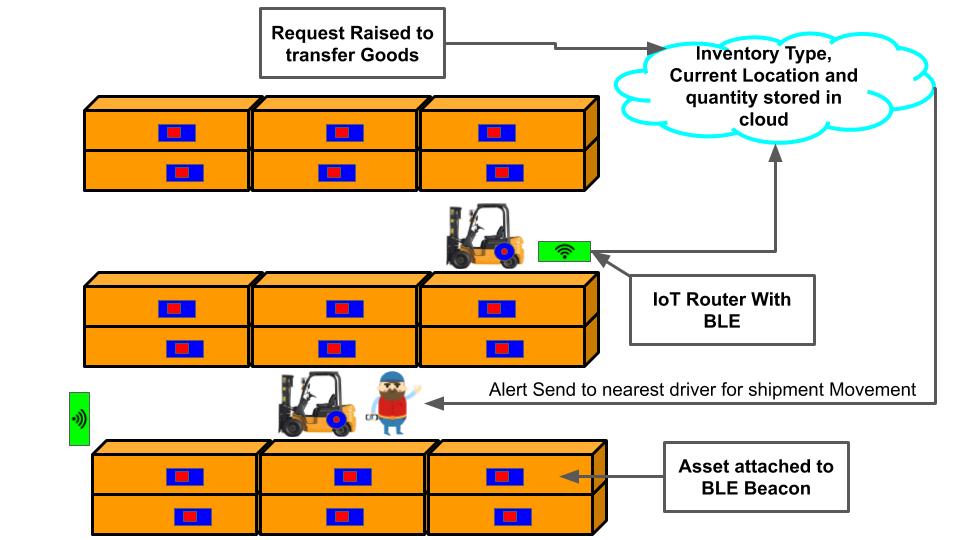
As shown in the above image, In a shipyard where containers are moved frequently using cranes. Managers provide instructions to move containers to the crane operators. This is done in an uncontrolled manner.
IoT solutions can improve crane utilization by providing real-time crane and container position data to the cloud. In this way when a container is required to be moved, the nearest crane operator receives the instructions. As a result, resources are used more effectively.
Restricted Access Control Using IoT Devices
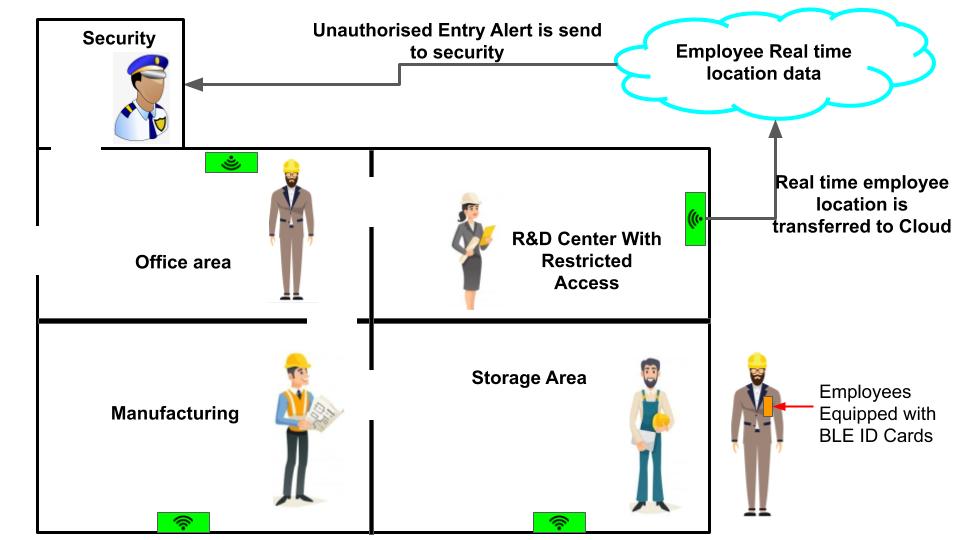
Conventionally authorized persons access Inside restricted areas is controlled by using RFID tags and fingerprint scanners. But with IoT enables solutions this can be controlled more effectively
As shown in the above image, IoT-enabled solutions such as connected RFID tags or BLE beacons are used to monitor real-time employee location in the factory or office premises. These sensors are programmed to raise an alarm in case of restricted entry.
3. IoT in Manufacturing Supply Chain Management
Manufacturing quality products is not enough, shipping those products to customers has equal importance and has an impact on product quality. For example, medical products such as vaccines have to be shipped at the recommended temperature.

As shown in the above image, IoT-connected sensors inside shipping containers are used to monitor and track shipment conditions such as temperature, air pressure, shocks, and vibration, etc. If shipping conditions are not satisfactory, an alert can be generated.
Advantages of IoT in Manufacturing?
IoT-connected sensors are used to monitor and integrate all manufacturing activities from raw material management to the finished goods. It brings manufacturing automation to the next level. Implementing IoT in manufacturing operations has the following advantages.
1. Data Visibility
Connected machines provide a great level of visibility on the production floor. Managers can access real-time manufacturing data using internet-connected devices such as mobile or laptops.
Extended reality technologies such as augmented reality, virtual reality, and mixed reality are also used to visualize connected machine data in a better way.
2. Improved Productivity and Cost Reduction
The availability of real-time data aids in the effective utilization of resources and asset management. In this way, overall productivity is increased and manufacturing costs are reduced.
3. Shorter Time to Market
The availability of real-time IoT data brings more transparency to manufacturing operations. This helps in reducing manufacturing, purchase, and transportation time. As a result, new products come to market faster.
4. Improved Safety
An array of connected sensors creates a safer work environment. For example, when sensors monitor machine and safety equipment real-time data. Response teams can act faster in case of an emergency.
To sum up, IoT is becoming an integral part of manufacturing and supply chain management. IoT in manufacturing has applications from marketing, shop floor, inventory management to supply chain management. It helps in reducing manufacturing costs and getting products to market faster. We suggest you read this article on the application of machine learning in manufacturing.
We will keep adding more information on applications of IoT in manufacturing. Please add your suggestions, comments, or questions on IoT in manufacturing in the comment box.
Add a Comment