Powder coating is a type of final finishing operation on metal and thermoplastic parts used in automobile, consumer electronics, and telecom products to improve part aesthetics and corrosion resistance. This article covers Various types of powder coating, powder coating process, and their advantages compared to liquid paint.
Powder Coating Process
Powder coating is applied to metal or thermoplastic parts electrostatically as dry powder. After the coating, parts are cured in the heat to allow powder to flow and form the skin.
Chromate conversion coating, zinc plating, and anodizing are used as base coatings to improve corrosion resistance. The powder coating process involves the following three steps.
- Cleaning and Pre-Treatment
- Powder Coating
- Curing
Step-1: Cleaning and Pre-Treatment process before Powder Coating
Metal parts cleaning before powder-coating is required to remove foreign particles such as rust, dust, and oil. The pre-treatment process improves powder coat adhesion properties and corrosion resistance to improve powder-coat quality.
Mechanical and Chemical Cleaning
Mechanical cleaning involves sandblasting and other abrasive actions to remove corrosion and other irregularities from the metal parts.
Whereas chemical cleansing utilizes chemicals to remove oil, dirt, and grease present on the part surface.
Pre-treatment Process
The Pretreatment process improves powder adhesion with the metal surface. Chemical etching and conversion coating improve metal adhesion properties and corrosion resistance. Following are the some of widely used conversion coatings.
- Iron Phosphating
- Zinc Phosphate
- Anodizing
Conversion coating has the following benefits:
- Improves the powder coating life.
- Adhesion of the powder coat with the metal surface improves.
- In-process corrosion protection.
Seven Tank Cleaning Process
Engineers recommend the Seven Tank process for the cleaning and pretreatment of metal parts.
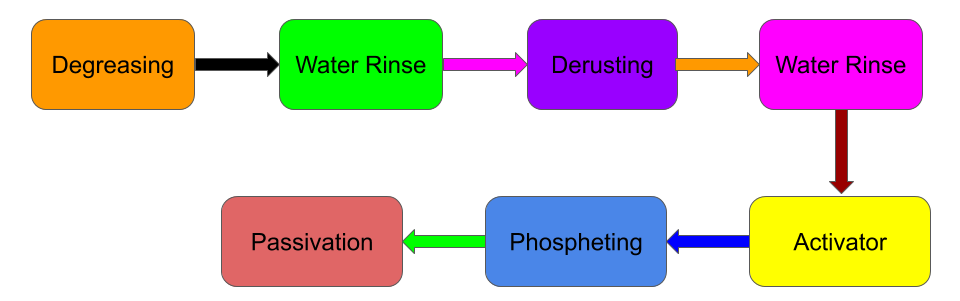
Step 2: Applying Powder Coating
Powder coating is applied to metal or thermoplastic parts electrostatically as a dry powder using an electrostatic gun.
Working Principle of Electrostatic Powder Coating

A coating gun charges powder with a positive charge, and parts to be powder coated are grounded. The powder gets attached to the part when sprayed towards parts using compressed air from the electrostatic gun.
Step 3: Curing
Powder coating requires curing at elevated temperatures (160º to 210º C for 20 minutes) in special ovens to cross-link the polymers. Convection and infrared radiation curing ovens are also available to cure powder coating parts.
Types of Powder Coating
The following types of powder coat are available according to dry powder chemical composition and its cross-linking structure. Each type of powder coating has its advantages and limitations.

1. Thermoplastic Powder Coating
Thermoplastics are synthetic materials that can form multiple times. High temperatures can melt thermoplastics. Therefore manufacturer does not recommend the thermoplastic type of powder coat for high temperature or heated environments.
But they have good wear and chemical resistance. The following types of thermoplastic powder coatings are available on the market.
1.1) Nylon
Nylon powder coatings are durable and impact-resistant and offer good protection against a wide range of chemicals, solvents, and oils. FDA-approved food contact grades are available. Nylon coating has applications in gears and conveyor equipment due to the low friction coefficient.
1.2) Polyester
The polyester coating has good adhesion, abrasion, and UV-resistant properties. Therefore it is recommended for outdoor applications such as furniture and automobile parts.
1.3) Polyvinyl Chloride (PVC)
PVC coatings are pliable, sleek, durable, and have good electrical resistance. FDA-approved food-grade PVC coatings are also available.
1.4) Polyolefin
Polyolefin powder coats are resistant to abrasives and chemicals. These coatings have excellent adhesion with a smooth surface finish. Polyolefin coatings have an application on components that require regular cleaning.
2. Thermoset Powder Coating
Thermoset types of powder coating create a non-reversible chemical cross-linking reaction that changes the powder coating physical properties.
2.1) Epoxy
Epoxy powder coatings provide a uniform and smooth appearance, are very durable, have excellent hardness, good chemical and corrosion resistance.
But epoxy coating fades and chalk when it comes in contact with the sun. Therefore they are recommended for indoor applications only.
2.2) Acrylic
Acrylic coatings are highly glossy, smooth appearance, and perform better than epoxy coating in sunlight. Clear or transparent acrylic coatings are also available in the market.
2.3) Epoxy Polyester Hybrid
Hybrid coatings are manufactured by mixing epoxies and polyesters. They have good mechanical properties, corrosion, and chemical resistance.
Hybrid coatings chalk less and have outdoor applications due to the presence of polyester.
Advantages of Powder Coating compared to Liquid Paint
Following are the advantages of powder coating metal parts compared to liquid paint.
- Do not contain volatile organic compounds (VOCs)
- Higher coating thickness is achievable compared to liquid paints.
- Uniform visual appearance across a coated area regardless of part orientation.
- Good scratch resistance, toughness, and hardness.
To sum up, dry powders are available in various materials, colors, and special effects such as stain, glossy, etc. They have applications in the automobile, telecom, and construction industry. Low temperature cured dry powders are available for coating thermoplastic parts.
We will keep adding more information on various types of powder coating and their applications. Add your suggestions, comments or questions on different types of powder coatings in the comment box.
Request you to share the Details of powder coating