Machining is a type of subtractive manufacturing process to manufacture machined parts by removing material from a workpiece using cutting tools. Various types of machining operations are available to machine material.
A workpiece can be a metal, plastic, wood, or ceramic material. Different types of machining operations can remove material from the workpiece in different ways. CNC Machines are used to machine workpieces more accurately with minimum operator intervention.
Types of Machining Operations
- Conventional or Traditional Machining Operations
- Turning
- Milling
- Grinding
- Drilling
- Plaining
- Shaping
- Broaching
- Non-Conventional or Non-Traditional Machining Operations
- Chemical-Machining
- Electro Chemical Machining
- Wire Cutting
- Electric Discharge Machines
- Electrochemical Grinding
- Ultrasonic-Machining
- Laser Cutting
- Water Jet Machining
- Abrasive Jet Machining
Traditional Machining Operations
The conventional machining process requires a cutting tool that removes material from the workpiece by coming in direct contact. Here are the different types of traditional machining operations.
Turning Operation
Turning is a type of machining operation used to remove material from the outer diameter of a cylindrical workpiece.
The workpiece is held in a chuck rotating at high speed during turning operation. A single-point cutting tool is fixed to the machine, and it moves in X and Y directions to cut the material.
We can use Lathe or Turning machines for turning operations. We can do the following machining operations on a turning or lathe machine.
- Turning
- Facing
- Parting
- Grooving
Milling Operation
In milling operation, a rotating mill cutter cuts the material from the workpiece.
The workpiece remains stationary during the milling operation. The cutting tool rotates and moves in X, Y, and Z directions to cut the workpiece. The following two types of milling machines are available in the market:
- Horizontal Cutting Milling Machine: The mill cutter is mounted horizontally.
- Vertical Milling Machine: The mill cutter is mounted vertically.
Grinding
Grinding is an abrasive machining process. It utilizes a grinding tool to remove small material (0.00635 to 0.0254 mm).
Manual and controlled grinding machines are available in the market. Lapping and sanding are types of grinding operations. We suggest you also check this article on high-quality grinding mills.
Drilling
Drilling is a metal cutting operation by rotating and pressing a multi-point cutting tool to cut a circular-straight-hole in solid materials. A Multi-point cutting tool is known as a drilling bit.
Standard drill bits in various sizes are available in the market. The drill bit is rotated at a very high rpm to drill a hole. Following operations are feasible on a drilling machine.
- Drilling
- Reaming
- Tapping
- Boring
- Counter-boring
- Spot Facing
- Countersinking
Click this link to know the various types of drilling machine operations.
Shaping Process in Machining
Shaping is a type of machining operation to remove material from flat surfaces.
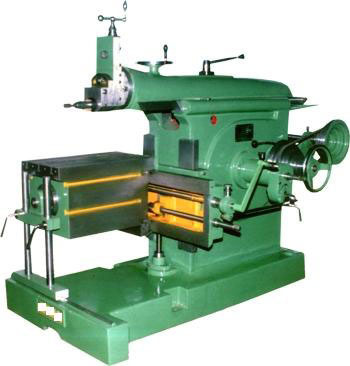
During the shaping operation, the workpiece remains stationary, and the cutting tool reciprocates to remove the material. A shaper machine can be a horizontal or vertical axis shaper machine.
Planing Machining Process
Planing is a type of machining operation used to remove material from flat surfaces and cut a slot. During this process cutting tool is kept stationary, and the workpiece reciprocates in its position.
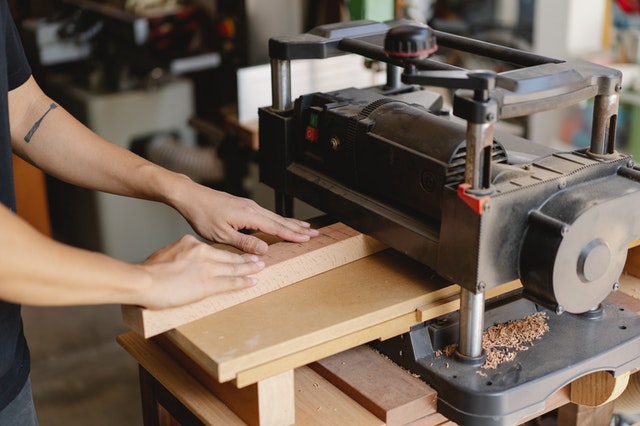
The planing process is similar to shaping operation. The difference in planing and shaping operation is in the way the cutting tool moves. During shaping operation cutting tool moves, and the workpiece remains stationary, whereas in planning operation, the cutting tool remains stationary, and the workpiece moves.
Broaching Operation
The broaching operation is a type of machining operation that utilizes a broach tool to cut the workpiece. The Broach tool is pushed or pulled in the workpiece using a broaching machine to cut the part.
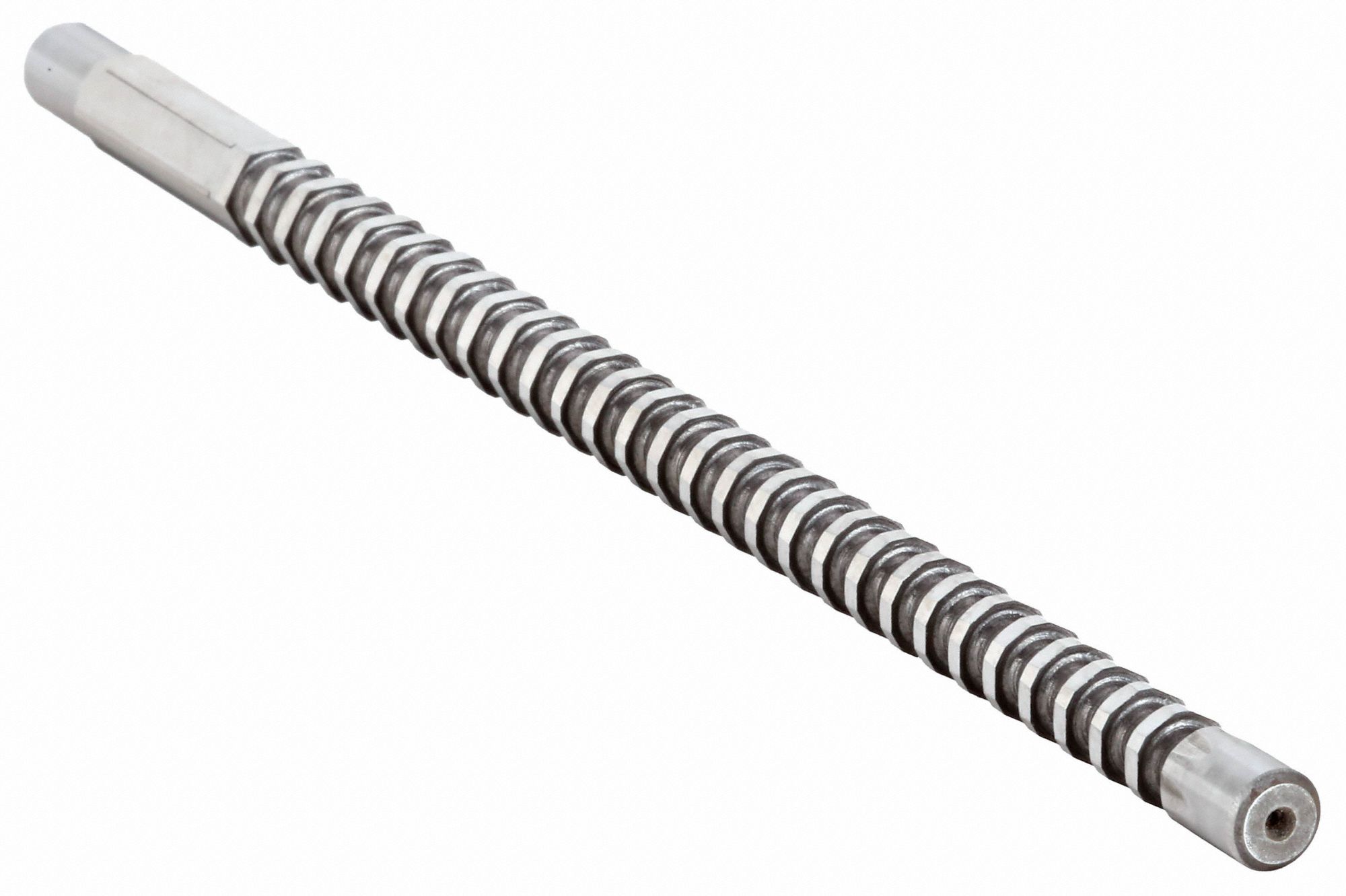
A broach tool is a cutting tool having a series of cutting edges. Broaching is used to achieve high dimensional accuracy and a good surface finish.
Non-Traditional Machining Operations
The non-conventional machining process does not require a cutting tool to remove the material from the workpiece. Therefore machines do not have direct contact with the cutting material.
Chemical Machining
The chemical machining process works on the principle of chemical etching. The workpiece is exposed to a chemical known as enchant during chemical machining process. The enchant removes the metal from workpiece due to chemical reaction.
Chemical machining process has application to manufacture precise and delicate parts such as electronics shields.
Electro Chemical Machining
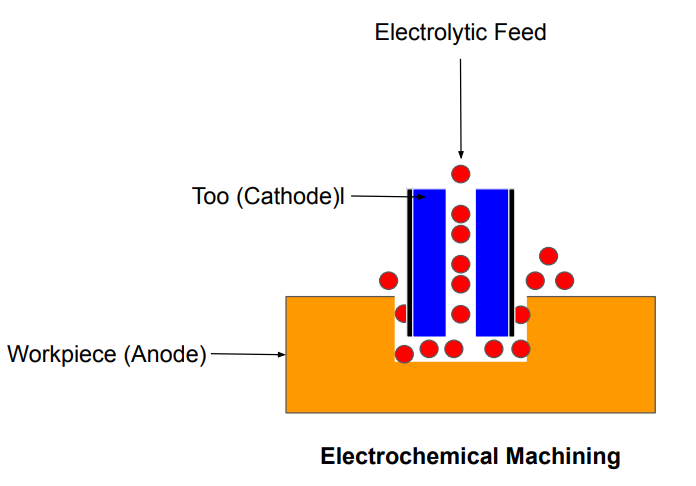
The Electrochemical machining process works on Faraday’s law of electrolysis. It is the reverse of the electroplating process.
The electroplating process deposits the material on the workpiece, whereas electrochemical machining removes the material from the workpiece.
Electric Discharge Machining
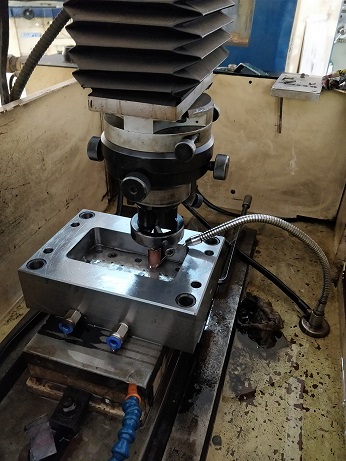
Electric discharge machining or EDM process removes material from a workpiece due to an erosion of the metal. The metal erosion occurs because of an electric spark between the electrode tool (cathode) and workpiece (anode) in the presence of die-electric fluid.
Wire Cutting
Wire cutting machining operation works on the same principle of EDM. During the wire cutting process, the wire does not comes in direct contact with the workpiece. It removes the material due to electric spark between wire and the workpiece.
Ultrasonic-Machining
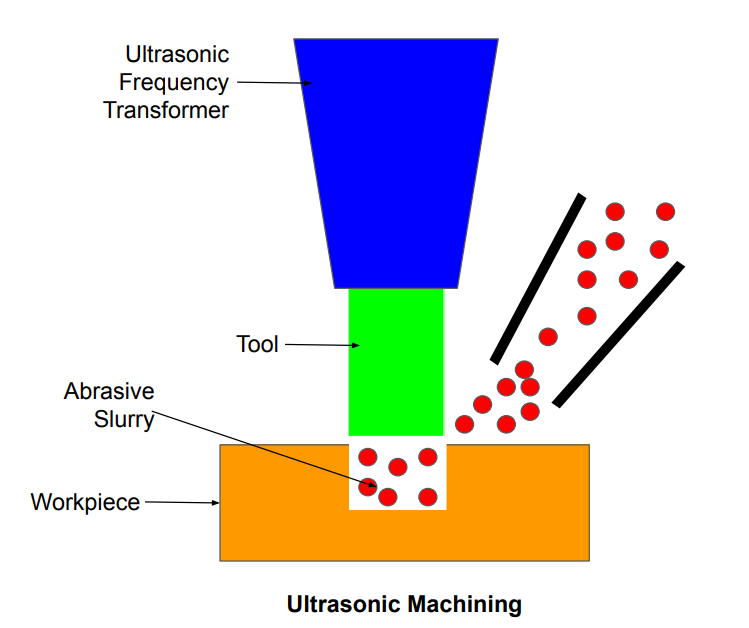
The ultrasonic machining process utilizes an abrasive slurry and vibrating tool to cut the workpiece. The tool vibrates at low amplitude (25-100 microns) and high frequency (15-30 kHz). We suggest you also read this article on ultrasonic welding process.
Laser Cutting
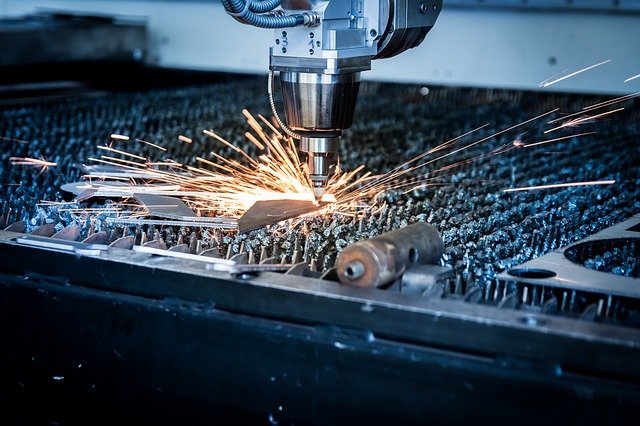
The laser cutting process utilizes a focused laser beam to melt the material from the workpiece. The laser cutting process utilizes a gas jet to remove molten material from the workpiece.
Water Jet Machining
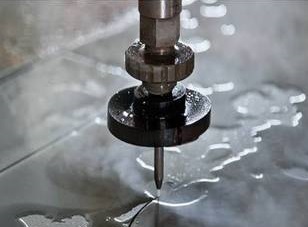
Water Jet Machining or WJM utilizes high-velocity water jets to remove material from the workpiece. WJM utilizes abrasives such as sand (SiO2), glass blend, and aluminum oxides to cut hard materials.
Abrasive Jet Machining
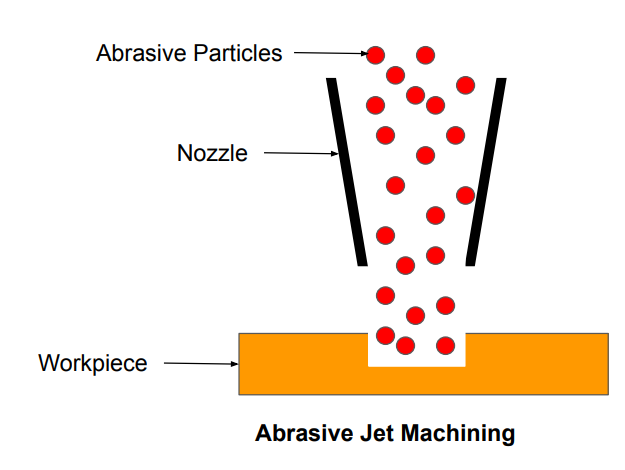
In abrasive jet machining, abrasive particles are mixed with gas or air. A high-speed stream of abrasive particles hits the workpiece surface to remove the material.
We will keep adding more information on Conventional and non-conventional machining. Please add your suggestions, comments, or questions on different types of machining processes.
Add a Comment