What is Sheet Metal Bending Operation?
The Sheet Metal Bending process involves the application of external force using a punch and a die at the specified length of the workpiece. This external force results in the plastic deformation of the workpiece. The type of bend and bend length depends on punch and die design.
This article covers various types of sheet metal bending operations and their applications. We suggest you also read this article on sheet metal cutting.
Sheet Metal Bending Methods
Following types of sheet metal bending methods are available according to sheet metal bend type, bend shape, and production volumes.
- Press-Brake-Bending
- Roll-Bending
- Deep Drawing
1. Press Brake Bending
Press brake or Brake Press in sheet metal parts utilizes v-types of flat punch and die to make straight sheet-metal bend at required angles. During sheet metal bending, the operator places the workpiece in a V-Die. In the die, the bending punch is pressed against the sheet metal workpiece at the bending line.
Sheet metal bending angle depends on the travel of punch against the sheet metal workpiece. And the internal bend radius depends on the punch radius. As a result, the operator can use the same punch and die to bend different sheet metal parts.

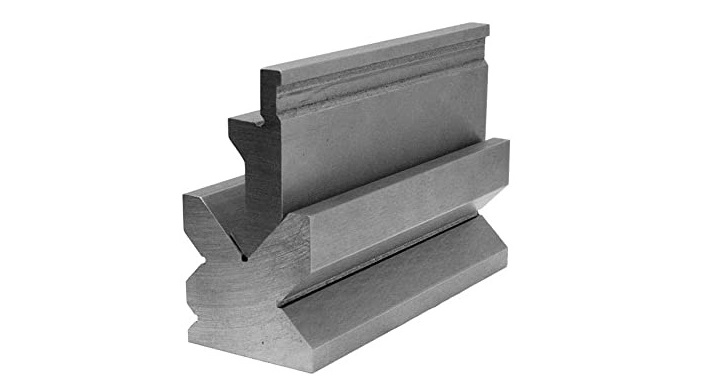
Brake press machines have applications to bend sheet metal parts with low production volumes. Because the same punch and die can bend different sheet metal parts. Press bending machines have applications in the following industries:
- Electrical and electronics enclosure.
- Racks
- Doors etc.
Different types of Press Bending Operations
Following types of press-brake bending operations are available. Each type has a different application.
- Air Bending
- Coining
- Bottoming
1.1) Air Bending
During Air bending operation the sheet metal workpiece does not come in contact with outside edges or the bottom of the V-die.
Therefore the inside diameter of the sheet metal part is controlled by V die Opening. The larger the v-opening, the larger will be the inside bend radius.
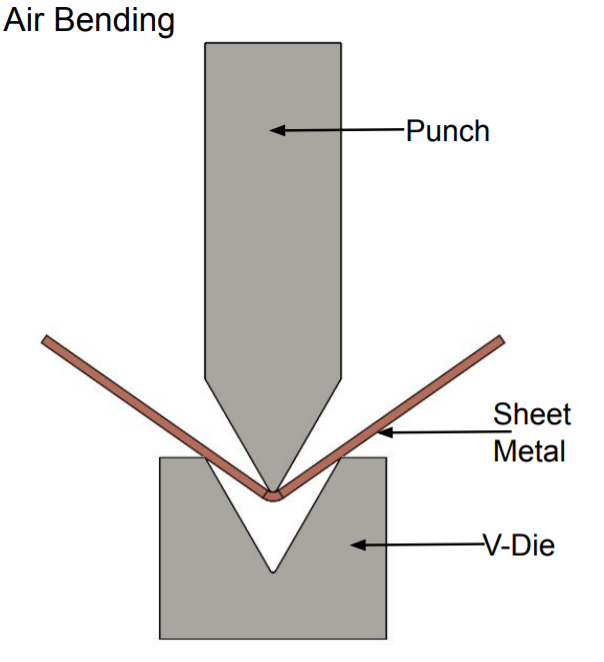
- The V-die angle should be greater than the bending angle of the sheet metal part. Because in the air bending sheet metal part does not come in contact with the die wall.
- In Air bending, the operator can control the bend angle by the travel of the punch.
- The operator bends the sheet metal part more than the required angle to compensate for spring-back in air bending.
1.2) Bottom Bending
Bottom Bending or Bottoming in sheet metal involves bending sheet metal parts such that the material makes contact with the punch tip and sidewall of the V-die opening. But punch and die do not make complete contact with sheet metal. In this, the sheet bend angle is equal to the V-Die angle.

As shown in the above image, the bottoming involves the following three steps.
Step-1: Place the sheet metal workpiece against V-Die.
Step-2: Sheet metal punch bends the workpiece up to the punch angle to compensate for the impact of spring-back. The punch angle is always less than the die angle. For example, to bend a sheet metal part at a 90° angle. 90° V-die and 88° angle punch are required.
Step-3: When the operator releases the punch from the part, the sheet metal part takes the angle equal to the die angle due to the spring-back action.
1.3) Coining
Coining in sheet metal involves bending a sheet metal workpiece using a punch and die such that the Punch penetrates the sheet metal part.
In this way, coining gives highly accurate and precise sheet metal parts. But the high impact of Punch and die can cause thinning in the bending region.

Advantages of Coining Sheet metal operation
- Highly accurate, precise, and repeatable.
- Can be performed on old or less sophisticated machines.
- Inside bend radius is equal to the radius of the punch.
- No spring back action.
Disadvantages of Coining Sheet metal operation
- High tonnage machines are required compared to air bending or bottoming.
- High tear and wear.
2. Roll Bending
Sheet metal Roll Bending Method is used for manufacturing tubes, cones, or other revolved sheet metal parts. It utilizes revolving rollers to apply force on a sheet metal part and form it in round shapes.


Minimum recommended bend radius For roll bending steel sheet is 1 to 3 times sheet thickness. Whereas, the minimum recommended bending radius for aluminum is 0.8 to 1 times sheet thickness.
3. Sheet Metal Drawing

Sheet metal Drawing Operation involves drawing sheet metal parts in a cup-like shape by utilizing a bending press. This process is very extensively used in the automobile industry to achieve a high production rate.
We can monitor sheet metal press online using a machine monitoring system.
Frequently Asked Questions: FAQ
The sheet metal drawing operation is the best way to manufacture high production volume sheet metal parts at the lowest possible cost.
The press bending method is the best way to manufacture sheet metal parts in low production volume. It also does not require any special tool development.
K-Factor, bend allowance, and bend deduction is used for sheet metal bending calculations. We recommend you to read this article for more details.
We will keep adding more information on various sheet metal bending operations. Add your comments, questions, or suggestions on different types of sheet metal bending processess in the comment box.
Add a Comment